- Makerbot Industries Port Devices Driver Download
- Makerbot Industries Port Devices Drivers
- Makerbot Industries Port Devices Driver Updater
- Makerbot Industries Port Devices Driver Windows 7
A customer attaches the equipment that needs to be fixed to a computer running HelpWire and shares the device with a few clicks. Step 2 — Operator An operator connects to the customer’s malfunctioning device over the network and gains full access to the equipment. Step 3 — Operator The expert diagnoses and fixes the device remotely. I installed Replicator software + drivers and still the same. I also installed the Makerbot software and same issue. On Windows in the device manager is always shows up as 'unknown device'. I even tried to update the drivers through device manager, pointing to the relevant folders containing drivers and it just says 'current usb driver installed'.
Enable Flexible Payments with ePort Cashless Solutions
ePort G10-S Kit
Modular cashless payment solution with Verizon 4G/LTE connectivity.
Payment Types:
EMV Contactless, NFC/RFID, Magstripe, Mobile Wallet, MORE Loyalty Card
Kit Includes:
G10 card reader and G10 telemeter
At a Glance:
4G/LTE Connectivity; Ultra-Fast Processing; Mobile Wallet Ready; Stored Value Compatibility; VMS Integration; Remote Monitoring
ePort G10 Pulse Kit
All the functionality you need, with all the features you want for coin-operated machines.
Payment Types:
EMV Contactless, NFC/RFID, Magstripe, Mobile Wallet. MORE Loyalty Card

Kit Includes:
G10 card reader, G10 telemeter, and pulse interface adapter
At a Glance:
4G/LTE Connectivity; Ultra-Fast Processing; Maximum Data-Capture; Stored Value Compatibility; VMS Integration; Remote Monitoring
ePort Interactive
Powerful interactive payment screens for greater engagement and sales.
Payment Types:
NFC/RFID, Magstripe, Mobile Wallet, MORE Loyalty Card
INCLUDES:
Integrated card reader and telemeter, touchscreen, and multimedia platform
At a GlancE:
Support On-Screen Nutritional Facts; Advertising with Interactive Interface; On-Screen Assistance; Ultra-Fast Processing; VMS Integration; Remote Monitoring
ePort G10-Chip Kit
Advanced security with EMV contact and contactless payment acceptance.
Payment Types:
EMV Contactless, EMV Chip-card, NFC/RFID, Magstripe, Mobile Wallet, MORE Loyalty Card
KIT INCLUDES:
G10-Chip card reader and G10 telemeter
At a Glance:
4G/LTE Connectivity; EMV certified; Ultra-Fast Processing; Maximum Data-Capture; Stored Value Compatibility; VMS Integration; Remote Monitoring
ePort G9 Kit
All of the functionality you need to accept Interac Flash in Canada.
Payment Types:
Interac Flash, NFC/RFID, Magstripe, Mobile Wallet
KIT INCLUDES:
G9 card reader and G9 telemeter
At a Glance:
Fast Processing; Supported in Canada; Maximum Data-Capture; Stored Value Compatibility; VMS Integration; Remote Monitoring
Seed Telemeter
Flexible legacy telemetry solution from Cantaloupe Systems.
Payment Types:
NFC/RFID, Magstripe, Mobile Wallet
At a Glance:
Fast Processing; VMS/Seed Integration
- 1PWM Driver v1.1
- 1.1Overview
- 1.1.1Get It!
- 1.2Files
- 1.3Interface
- 1.4Circuit Board
- 1.5Test Your Board
- 1.6History
- 1.1Overview
Overview
<div></div>This board is designed to allow you to control high power devices that only have a single polarity. Things like heaters, fans, solenoids, and even motors (you can only turn them in one direction, however.) It takes PWM (pulse width modulation) inputs from a microcontroller such as an Arduino, and amplifies them into high power outputs. It has 3 channels on each board, and can drive up to 5 amps on each channel with the proper heatsinks.
- You'll need a soldering toolkit to do most of this.
- Read our Electronics Fabrication Guide if you're new.
Get It!
Full Kit
Raw Components
The link above doesn't work any more, so here is a parts list sussed from the schematic and instructions:
Amount | Type |
4 | 560-ohm resistors (R4 - R7) |
3 | 1k-ohm resistors (R1 - R3) |
3 | 1N4004 diodes (D1 - D3) |
4 | standard(?) LEDs (LED1 - LED4) |
1 | 100 nF capacitor '104' (C1) |
1 | 100 uF capacitor (C2) |
1 | hard drive power connector |
3 | output headers (X4 - X6) |
3 | TIP120 power transistors (T1 - T3) |
Files
<div></div>You can download the release file from SourceForge that has a bunch of helpful files for this board. It contains:
- GERBER files for getting it manufactured
- PDF files of the schematic, copper layers, and silkscreen
- Eagle source files for modification
- 3D rendered image as well as POVRay scene file
Schematic
<div></div>Interface
Makerbot Industries Port Devices Driver Download
Input
The PWM Driver has 4 input pins:
Pin | Function |
PWM1 | Send a PWM signal from the Arduino directly to this pin to control channel 1. 0 = off, 255 = maximum. You may also be able to use a digital out pin to control it as on or off |
PWM2 | Same as above, but for channel 2 |
PWM3 | Same as above, but for channel 3 |
GND | It's recommended to connect this to the ground on your Arduino to share a common ground. |
POWER | This is a power input connector. We use a polarized disk-drive style power connector found on nearly every ATX power supply in existence. If you want to directly connect your own power, the board requires 12v input. |
Output
Each channel is rated to drive up to 5 amps. Whether or not your heatsinks and power supply are up to the challenge is another story. Give it a try and let us know if you can break it!
Pin | Function |
channels 1-3 | This is the output for the respective input pin. Each set of outputs has two pins: a positive and a negative. When you hook up your device, you need to double check to ensure that you have the polarity correct. Not doing so could result in your device going poof. |
Circuit Board
<flickr>2172341901</flickr>
You can either buy this PCB from the RepRap Research Foundation, or you can make your own. The image above shows the professionally manufactured PWM Driver v1.0 PCB ready for soldering. Its also cheap, only $5.00 USD.
Components
<div></div><iframe src='http://parts.reprap.org/embed/module/PWM+Driver+v1.1' width='600' height='500' frameborder='0'>Visit http://parts.reprap.org/embed/module/PWM+Driver+v1.1</iframe>
Known Bugs
The back EMF protection diodes are in the wrong place. Where they are at the moment does not provide any protection from inductive loads. They should be wired anode to the transistor collector, cathode to VSS. See [[1]]-- Main.ChrisPalmer - 10 Dec 2009
If you find any more, please contact us in the forums.
Build Process
<div></div>Solder R4-R7 green-blue-brown
These are the 560 ohm resistors. There are 4 of them. They can be soldered in any orientation. Polarity doesn't matter. When you are done, clip the long wires sticking out close to the board.
Solder R1-R3 brown-black-red
These are the 1k ohm resistors. There are 3 of them. They can be soldered in any orientation. Polarity doesn't matter. When you are done, clip the long wires sticking out close to the board.
Solder D1-D3
These are the diodes to protect the circuit when driving motors and such. There is a stripe on one end of the diode which corresponds to a stripe on the silkscreen. Make sure the diode is oriented in the same direction as on the silkscreen and solder it in. When you are done, clip the long wires sticking out close to the board.
Solder LED1-LED4
These are the LED's to tell you when the power is on, as well as when each channel is active. Simply line up the flat side of the LED with the flat part of the silkscreen and solder away! It is important that you insert them in the proper orientation. They will not work otherwise. When you are done, clip the long wires sticking out close to the board.
Solder C1
This is the yellowish, circle shaped capacitor in the picture, though yours may not be either yellow or circle-ish. It may even be cryptically marked '104'. Solder it into the rectangular area reserved for it. The polarity or orientation doesn't matter. When you are done, clip the long wires sticking out close to the board.
Solder C2
This is the cylindrical black and grey capacitor. It has a negative and positive side. The silkscreen has a + sign where the positive side is supposed to go, and the capacitor has a - sign along its negative side. Insert the capacitor accordingly and solder it in. When you are done, clip the long wires sticking out close to the board.
Solder the Power Connector
The power connector is the same one as you find on hard drives in a computer. There are angled parts on the inside of the connector that match up to the markings on the silkscreen. Insert the part according to those, and then solder it in.
Solder X4-X6 (output headers)
These are the output headers that you'll plug whatever device you want to power. Solder the headers with the tabs facing towards the inside of the board. The silkscreen has a top-down representation that should help you if you are confused. Insert the part, and solder it in.
Solder T1-T3
These are the power transistors, and they are what turn the signals from your microcontroller into high current to power your devices. Solder them with the flat heatsink tab facing outwards. After you are done, you can bolt a strip of aluminum to them (or use real heatsinks) During soldering they may come out of alignment, so it could be sort of tricky. It is probably a good idea to fit a heatsink to the transistor that will drive the RepRap heater coil as that has to dissipate about 4W.
Solder input wires
Take about 2 feet of the wire from a Cat6 ethernet cable, and take 2 twisted pairs from that. If you want to use the official color scheme, take the orange and brown pairs. Strip about 1/4 inch from the ends of each wire, and solder them into the input holes. You will want to match them up like so:
Color | Input |
White/Orange | PWM1 |
Orange | PWM2 |
White/Brown | PWM3 |
Brown | Ground |
When you are finished, twist all the wires into a single cord to keep things tidy.
You have now completed soldering your PWM Driver Board! Do a happy dance and get ready to see if it works.
Test Your Board
Now we have to test the board. Its very easy, and consists of a few steps.
IMPORTANT:
- Always turn power supply off before making/breaking connections.
- Always turn your power supply off before plugging it in. It won't fry things most of the time... but all it takes is once to damage things.
- Its a good idea to ground yourself before touching components. You don't want to fry anything.
Test Power on PWM Board
<div></div>Simply take your hacked PC power supply and plug a power connector into PWM board. Once you turn the power, the power LED indicator should come on.
Wire up test devices
<div></div>I prefer using a computer case fan (preferably with LED's) but any sort of DC device you can find laying around will do: motor, light, etc. You could even make do with a resistor and a LED. You'll need 3 of these to test it easily, but you can make do with one if you feel like swapping it to test the other channels.
Once you have your devices, wire them each up individually to a channel. Make sure you get the polarity right. In the example of our fans, they probably just won't turn, but if you use a different object it might not like it, so be careful. (eg. destructo)
Connect PWM Driver to Arduino.
This part is very easy. Strip 1/4' from the end of the input wires (You used Cat6 ethernet innards right???) Now, insert the end of each input into the correct pin on the arduino, and then connect the Ground pin to Ground on Arduino. Use the table below to determine what pins to hook up to what:
PWM Pin | Arduino Pin |
PWM1 | 9 |
PWM2 | 10 |
PWM3 | 11 |
GND | Ground |
Upload Firmware to Arduino
<object type='application/x-shockwave-flash' width='400' height='300' data='http://vimeo.com/moogaloop.swf?clip_id=345954&server=vimeo.com&fullscreen=1&show_title=1&show_byline=1&show_portrait=0&color=01AAEA'> <param name='quality' value='best' /> <param name='allowfullscreen' value='true' /> <param name='scale' value='showAll' /> <param name='movie' value='http://vimeo.com/moogaloop.swf?clip_id=345954&server=vimeo.com&fullscreen=1&show_title=1&show_byline=1&show_portrait=0&color=01AAEA' /></object>
Now, feel free to turn on the power to your power suppply. Next, open the Arduino software, and copy/paste the code below into it. Upload the code to your Arduino.
Once the program is compiled and uploaded, the Arduino will restart and run the exerciser code. The basic execution of the exerciser code goes like this:
- Gradually take all 3 channels up to maximum, then back down again.
- Gradually take each individual channel up to maximum and back down again.
- Repeat.
Troubleshooting
First, if the LED lights up and the fan does not, then check the orientation of the fan. If there are still problems, you will need to check your soldering, double check component placement and orientation, and finally if all else fails, post in the [forums for help and we'll try our best. If you can post pictures of your boards and setup, that will help us out tremendously.
History
Makerbot Industries Port Devices Drivers
Changelog
- changed to screw terminal outputs
- laid out board a bit better
Previous Versions
Makerbot Industries Port Devices Driver Updater
- An incremental improvement of the PWM Driver v1.0
- Which is loosely based on parts of the Extruder Controller v1.2
Makerbot Industries Port Devices Driver Windows 7
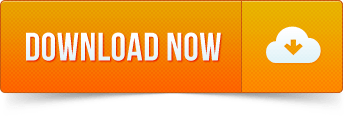